What is Reverse Engineering?
Reverse engineering is the process of extracting and analyzing information from a physical part in order to gain an understanding of how the product was created, designed, and produced.
Reverse engineering is valuable to product design and development in many ways:
- Replicate a part that is no longer in production and don’t have the design documents
- Scan prototypes for testing and validating the design prior to production
- Improving an existing product through design modifications
- Create complementary products that need to fit perfectly with the part (cases, accessories, product packaging)
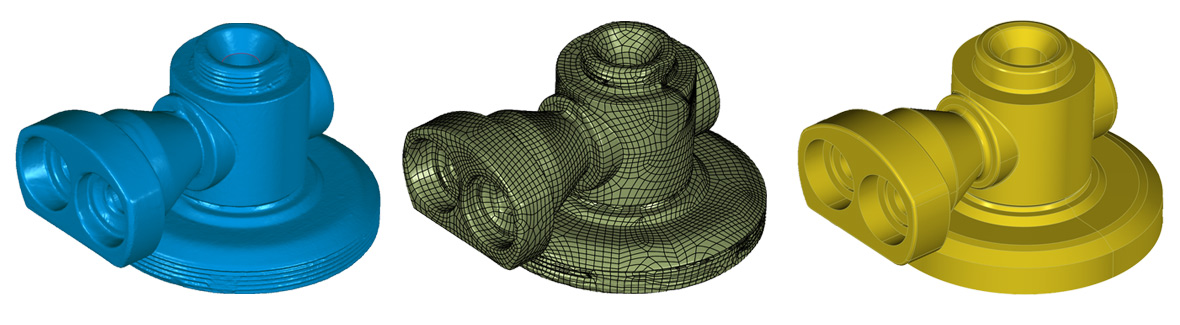
Applications dedicated to reverse engineering distinguish themselves from general CAD tools by extracting all dimensions and parameters from the scan data. Using sections from the point cloud, sketch curves can be used to extrude, revolve, loft, and blend. Constant feedback on the fidelity of the newly created CAD model to the original scan ensures greater accuracy while following the larger design intent. The workflows are familiar to CAD users and result in “smart” solids that can be modified via parameters. These models can be invaluable when converting from a tried and tested prototype to a final run part design or when re-creating tools and molds in-hand which do not have digital definition available. Parametric modeling is especially applicable to parts that have a majority of prismatic features such as planes, cylinders, fillets, rounds, etc.
The other method of reverse engineering developed after years of R&D is the fully automated or semi-automatic creation of a static solid that digitally duplicates the mesh from scans. Sometimes referred to as a “shrink-wrap” or “hair net”, the resulting surfaces stitch into a CAD solid that captures the as-built state of the object but is easier to use than a large cloud of discrete points. This mode is especially useful for freeform geometry such as bones, teeth, sculptures, and custom-fit molds. These shapes are found in field related to aesthetics, ergonomics, and fluid or aero-dynamics; essentially anything that the “forces of nature” have defined as the optimal shape.
Reverse Engineering Services
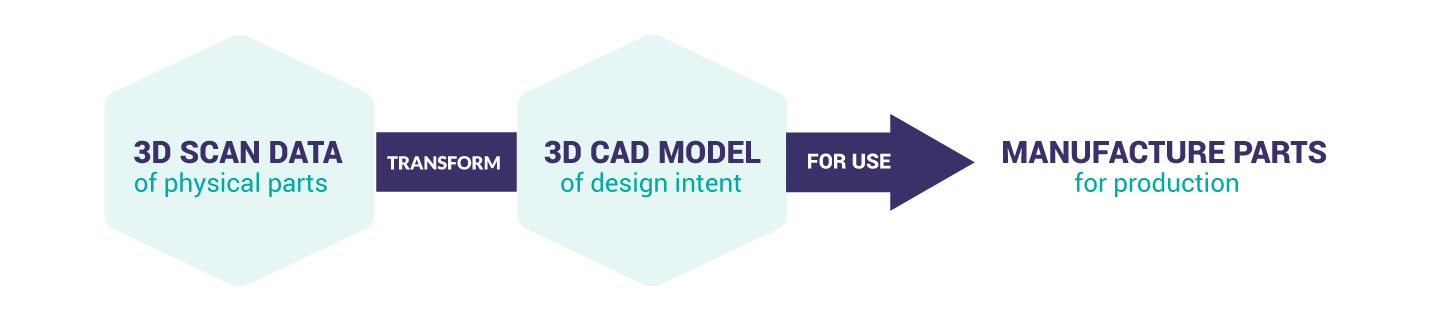
At Innovia3D, we can start from physical part by 3D scanning it or use scan data that’s already been developed through other means. We can deliver either a dynamic or static solid in a variety of formats as required. Our team assists designers and engineers in product development stage so products can reach to market at a faster pace. We specialize in using 3D scanning to capture 3D data of complex organic surfaces relatively quickly with a high level of detail and accuracy. Once the digital 3D model is obtained new features can be added and imperfections can be edited and modified using specialized 3D scan data processing software. When the design intent is satisfied, a computer-aided drawing (CAD) model produced for manufacturing. CAD is the standard format for manufacturing the part for production. The model will meet agreed specifications for accuracy and detail. There is no inherent size limit to the subject part, and we have experience doing parts as small as pen caps and control buttons and as large as aerospace and automotive structures.
Ask Our Specialist
Contact us to discuss how we can help you with our reverse engineering services.
Contact Us